The Shop: Building Tools for Designers to Thrive
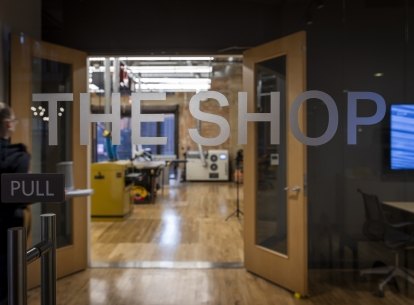
Dylan Wells, Director of Corgan’s model and fabrication facility — The Shop — has been building his team and services over the last five years. To keep up with the firm’s growing demand for fabrication and model making, The Shop recently expanded to a larger space in a new location in Dallas’ Historic West End. In this Insight, Dylan sits down to discuss The Shop’s evolution, and how this valuable resource positively impacts Corgan’s clients, architects, and designers.
Tell us about The Shop and how it evolved to what we see today and how you became involved.
Corgan believes model making is a valuable element in the design process and the firm has always maintained a model shop. When we expanded the Dallas office in 2019, the firm decided to invest more heavily in model making to show models to our clients. Since then, the shop has incorporated new technologies and has evolved into an integral part of our services. We’ve now expanded to our new 3,000 square foot space in the West End just three blocks from our Dallas office which will offer more resources to allocate to other projects — a strategic move for the firm going forward.
Previously, I worked in Corgan’s Aviation Studio and what I love about my job is fully diving into translating digital designs on a screen into reality and moving from the digital to the tangible. Getting to touch and feel it is a joy for me. I've always been a woodworker and maker, so this is an amazing endeavor I get to be part of.
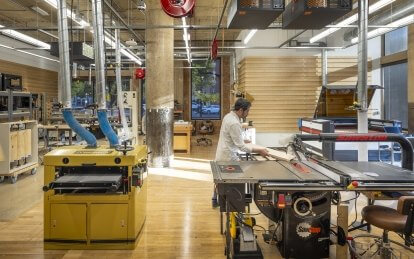
How would you describe the new shop?
The shop exists to bring designs to life through craftsmanship and fabrication. What we do is provide the resources, know-how, and skill sets to leverage traditional craftsmanship, woodworking, and hand tooling merged with some of the innovative computer-driven technologies we see in digital fabrication that let machines handle the tight tolerance work. We want to live in that beautiful merging of the two to create quality products that help us sell our great design work.
We've expanded our resources in both directions – there is a pairing of traditional and technology tools. We've acquired extensive digital fabrication tools like laser cutters, CNCs, FDM, and SLA resin printers as well as robust woodworking and tooling items such as a joiner planer, drum sander, table saw, and miter saw -- all the tools to be high-quality makers showcasing excellent design.
Why do we need physical models and how do they support architects and designers?
We're in such a digitally saturated world, not only with computer screens and digital software, but also with augmented reality (AR) and virtual reality (VR). I feel digital saturation is a bit of a disservice to designers, making them feel far removed from elements within the physical space. The value-add from producing the most basic, small-scale physical model ─ instead of just providing a client renderings or explaining the direction ─ is exponential. When clients see a 3D model, they love it. It becomes a conversation starter supporting collaboration between the client and designer, prompting valuable discussion and exchange of ideas.
I've heard many accounts of client meetings that present all these wonderful renderings, graphics, and diagrams, but when placing a model at the center, the client loves to engage with it — see it, touch it, feel it — and get that tactile responsiveness they don't get from a computer screen.
This not only happens on the client side ─ as soon as we put a model in front of our designers, they also too go crazy for it. There's something about human nature that loves seeing something go from the digital to physical form in front of their eyes.
Honestly, we make cool stuff for our clients, but supporting the phenomenal designers in our studios and developing the sense that they are “makers” is the biggest value-add for me. Many already embrace that as architects typically like to make things and fiddle with stuff. We want to enhance, equip, and train them to do that as often as possible.
Is there a certain point in the design process when models are most often used?
The beauty of models is that they are useful throughout the entire construction process -- from the initial proposal, schematic design (SD), design development (DD), all the way to client approval. Most of it gets down to scaled models. There are also mock-ups, staging, fabrication, and model making ─ all of which are relevant throughout the design process.
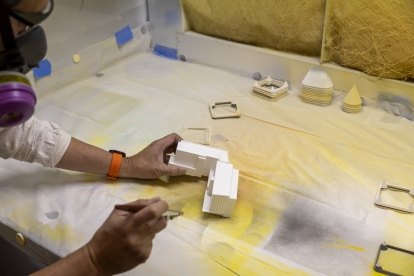
Can you talk about what you mean by mock-ups? Are they on a one-to-one scale?
One thing we're really excited about are the expanded resources - we not only make scale models of our design work, but can also provide the tools, resources, and expertise to illustrate installations and construction plans, which are especially valuable to contractors and clients. We get clients away from the digital screen to show them the actual items in real-time, at real scale, and in full operation, bringing it to life. This results in positive responses and hopefully assists in making tough design decisions.
How does our shop compare to larger firms and industry standards?
Fortunately, in architecture, model making is very relevant to what we do to showcase our designs, explore new ideas, and support the designer-client relationship. Model shops are not atypical to architecture firms, this one included. The benefit we offer is having identified this value-add at an opportune time. Rather than building a small shop and having to outsource equipment, or a large shop that's not right-sized and underutilized, we have allocated the appropriate resources to create anything from scale models to woodworking tasks in all stages of the design process. Our goal is to say ‘yes’ to our design teams and provide the resources and space necessary to get to that yes.
What is the list of services The Shop provides?
We can support architects and designers in every way possible when it comes to fabrication. One thing we've tried to do with the tools we either currently have, or will expand to in the future, is to be a one-stop-shop for whatever request fabrication-wise designers ask for.
We do it all. If the designer wants a master model produced in the mid to early stages and needs iterative explorations. We have the skill set to do that in mixed media. Let's say in the end they want a one-to-one mock-up -- we can handle that as well. It's all about trying to get that close pairing with the design team so we can support them with what they need, whether it be proposals or innovative solutions, we offer these services in-house, so their workflow is seamless and efficient.
We are the go-to resource for anything fabrication-related that comes through the door, whether it’s 3D printing, laser cutting, robotics, CNC routing and milling, painting, professional finishes, or any kind of woodworking task including joining, cutting, finishing, and sanding. We offer robust resources and experience to handle many different requests.
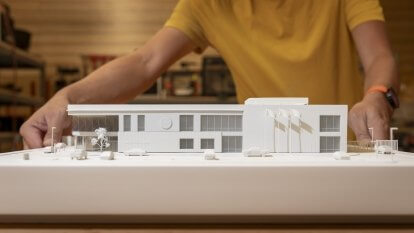