Initiative 99 — A Global Architecture Competition

The news has been filled with headlines about just how unaffordable the housing market currently is, especially for first-time homeowners, with the majority of houses in most cities out of reach for most residents. For extremely low-income households, the situation is especially dire, with a 14 percent increase in the shortage of available, affordable rental homes between 2021 and 2022. Texas in particular is one of the worst states for extremely low-income renters, with Austin, Dallas, and Houston ranked as the 3rd, 4th, and 5th worst cities in the country for affordable housing. Around 1 in 5 households in Texas are extremely low income, and nearly 4 in 5 spend more than half of their income on housing and regularly have to choose between paying rent and necessities like groceries, healthcare, and utility bills.
In the heart of Austin, Texas, where the struggle for affordable housing is pronounced, we embarked on a mission to redefine what it means to own a home, particularly for single mothers in low-income communities. A staggering 42 percent of low-income families are led by single mothers, who face hurdles that extend beyond housing. It isn’t just about shelter: providing a safe, comfortable, stable home for a family to live in long term has a profound impact on building relationships, establishing a strong foundation for children, and putting down roots.
The ICON Challenge
To address the challenge of stable and affordable housing for low-income households, ICON, a pioneer in 3D-printed homes, set the Initiative 99 challenge, “a global architecture competition aimed at designing accessible, beautiful, and dignified 3D-printed homes that can be built for under $99,000.” The use of 3D-printed concrete construction makes the construction more affordable and presents opportunities for long-term operational cost reduction, which is of utmost importance for low-income households. After reviewing the demographics of Austin, the Corgan team found that North Central Austin has the highest number of families living in poverty and the lowest median income. To have the biggest impact, the team selected this region as the site for their Initiative 99 design.
Building context
Understanding the ripple effects of the lack of stable affordable housing on both the mothers and their children, the project's primary focus became clear: to provide a home with dignity. To achieve this, the design process commenced with an earnest effort to understand the needs and desires of single mothers in Austin’s low-income communities. Through extensive interviews with 32 single parents, we sought to comprehend their living situations, ideal home features, community expectations, and the support systems they rely on. The quantitative and qualitative results from these interviews were instrumental in guiding the design process.
My kids need space ─ I can be fine in, you know, confined rooms, but they need space to have friends over. And need personal space too.
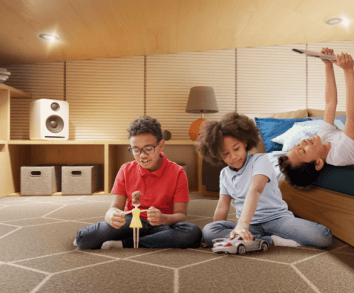
Our team found nearly 80 percent of single parents work full-time and half of the parents commute to work every day. Of the parents interviewed, the majority have one child between the ages of 0 and 12, while 30 percent have two or three children. Parents talked about how they use their homes – the living room was the most-used space – and what they would ideally include – a home office and utility room being the top two options. They also shared what they want to be able to provide for their children – words that came up frequently were peace, comfort, and safety. This input was vital in developing a house that provides low-income families with dignity, stability, and a place they are proud to call home.
Making a house a home
The insights gleaned from our interviews served as the foundation for the team, and we began designing a home that reflected the perspectives and needs of its future inhabitants. We wanted to acknowledge that a house is more than just shelter; it is a place of comfort, identity, safety, and future planning. Each step of the way, the design was refined according to input from the mothers. The basic footprint of the house is a 396-square-foot, single-story building that meets the cost cap set by the competition.
Affordable homes’ curbside presence is always so small, so they stand out. I don’t want to stand out.
First, to mitigate the stigma of affordable housing, we elongated the homes to increase the curb appeal and presence of the home. Since 90 percent of respondents prefer a private backyard, the rectangular footprint was bent to create a secure "hug" around the backyard offering mothers a view to their children at play. Acknowledging the diversity of preferences among single mothers, our team incorporated features such as semi-visible front doors and multiple entry points for safety. The design provides views that cater to the need for surveillance of the street, the children, and the community.
The next step in the design process was optimizing the interior layout to accommodate a growing family: children that will go from playing in the living room to needing a place to do homework, a toddler who loves co-sleeping to a teen who needs their own space, a mother who works from home during the day and hosts friends and family for dinner at night. Parents identified storage, children’s play area, and children’s sleeping area as the three most important spaces for their homes. They also greatly preferred a customizable interior and the ability to decorate and renovate as needed, so they can feel truly at home.
I feel most at home when I can have friends and family over. Hosting dinner parties, my son inviting over his friends from school — that really helps when he is doing homework.
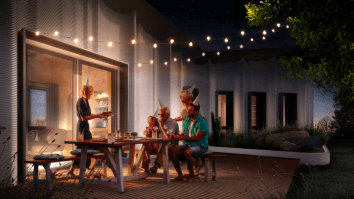
To keep the parents involved in the design, we sought feedback from them as the footprint was developed to see what did and did not work. In our initial plan, the outdoor space and open layout were popular, but parents did not feel safe with the front door near the bedroom and wanted more storage to keep things organized. The original layout was reworked according to this feedback – more storage was added, the bedroom area was tucked into the back corner of the home, and we opened up the active living spaces to the backyard and communal walking trails to keep the “village” close by.
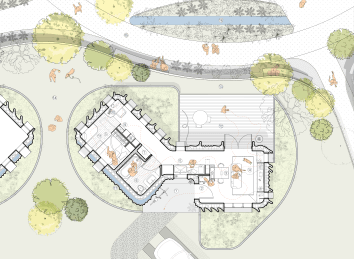
The final floorplan makes the most of the small footprint with a foldable table that can transform the living area to a dining room, a lofted area over the mother’s bed for the children’s room, a small study area tucked into a quiet corner, and a galley kitchen separating the living and sleeping areas. The front porch and drop zone lead to the central living area, which opens up onto a large back porch and private backyard, with access to the community walking trail and bioswale.
It’s easier being green
Efficiency was a key consideration in the design, with a focus on natural ventilation, heat reduction, water conservation, and solar energy generation. In addition to being more sustainable, the design helps to address parents’ concerns about high energy bills and ensures the long-term viability of the home for low-income families. After hearing from parents how difficult balancing monthly expenses is, we examined every aspect of the design to maximize efficiency and reduce monthly energy costs as much as possible to help lighten the load.
I don’t want to have to choose between paying my energy bill and buying groceries for my family.
The team oriented the building to capture prevailing winds, designed a solar deflection façade with optimized fins, and integrated a water wall that served dual purposes of insulation and rainwater collection. Because of the easily configurable nature of 3D-printed walls, the fins can be angled to deflect the most sun regardless of the site orientation, reducing the amount of heat brought into the house and reducing the amount of cooling needed. In total, the solar insolation results in a 32 percent decrease in heat gain.
The house's reliance on energy-efficient appliances and use of a ductless air source heat pump for water heating and air conditioning further contributed to its sustainability. Additionally, a 600-gallon sloped water tank is embedded within the 3D-printed façade that captures rainwater and feeds into restroom plumbing fixtures, saving up to 5,672 gallons of water annually. Other sustainable features include a photovoltaic system, ceiling fans, Energy Star rated appliances, and LED lighting. The team even sourced native plants for the landscaping that reduce humidity, purify the air, and require little water. Overall, the cost of energy expenses is reduced from $828 per month to $216 per month for water, electric, and heat.
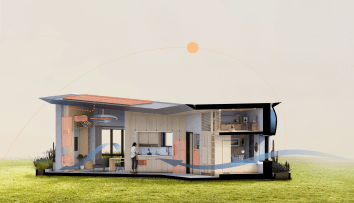
By leveraging modular prefabricated construction techniques, our team ensured a smooth and weather-independent construction process, with locally sourced sustainable materials and a high level of customization. The interior assembly process is assembled off-site using locally sourced yellow pine, a LEED qualification. Overall, the prefab construction of the interior modules means the houses can be built twice as fast, with 90 percent less waste, and 20 percent less cost than traditional construction methods. It also allows for mass customization, so the modules can easily be adapted to work for a nuclear family, a single person, or roommates – without changing the 3D-printed exterior. In addition to the cost-saving benefits for occupants, the design will be carbon negative after a decade, meaning it removes more carbon dioxide from the atmosphere than it emits.
It takes a village
Many of the mothers we spoke with talked about how important it is to have a community – a village – to pitch in when raising a family as a single parent. Understanding that a home is not just confined to its physical structure, we expanded our attention to the layout of the surrounding neighborhood. The qualitative insights from our interviews emphasized the desire for belonging, friendship, and comfort in a safe, helpful neighborhood.
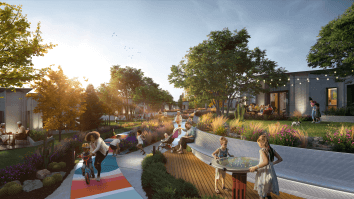
Community is the sense of belonging with the people around you; the people that raise you when times are tough.
To foster this needed support system, communal shared spaces were strategically integrated, creating a sense of connection and support for single mothers who often lack community backing. The masterplan includes an outdoor gym, communal garden, play area for kids, skate park, co-working facility, wellness center, amphitheater for community events, and bodega. Bioswales and walking paths further enhanced the community's sustainability, functionality, and aesthetics, elevating the project from just a house to a home.
Staying Agile
By looking at the longstanding challenge of building dignified affordable housing that is responsive to a growing family’s needs through the relatively new lens of 3D printing, our research and design team learned a lot. We learned about the 3D printer’s capabilities and potential limitations as a typology. We learned how we can design and shape a building to harmonize with the environment. We figured out how to maximize energy efficiency to minimize utility bills. As we look ahead, we’re eager to continue researching how additive manufacturing and modular prefabricated construction can help solve old problems – or new ones.